The design process has evolved dramatically in the last decade, and 3D printing stands at the forefront. For product designers and development teams, integrating 3D printing early and strategically into the design workflow can unlock significant advantages. Whether you’re a startup working on your prototype or a seasoned manufacturer refining a product, 3D printing can help reduce costs, speed up iteration, and push creativity to new heights.
In this article, we’ll explore how to integrate 3D printing into the design process, ensuring maximum impact for your projects.
Conceptualization: Bringing Ideas to Life Quickly
In the initial stages of design, ideas are often abstract. Traditional design processes rely on sketches or digital renders, which can feel limiting. This is where 3D printing can shine. By creating a simple physical model from the outset, you gain a tangible perspective on your concept that’s hard to achieve digitally.
Steps to Implement:
- Start with basic models in low-cost materials like PLA to get a feel for the form and proportions of your design.
- Consider printing a series of small-scale models that reflect different variations of your idea. A physical version can reveal ergonomics, size, and usability insights.
Benefits: Early-stage prototypes help you visualize the design better, assess feasibility, and make immediate changes without waiting on expensive or time-consuming production methods.
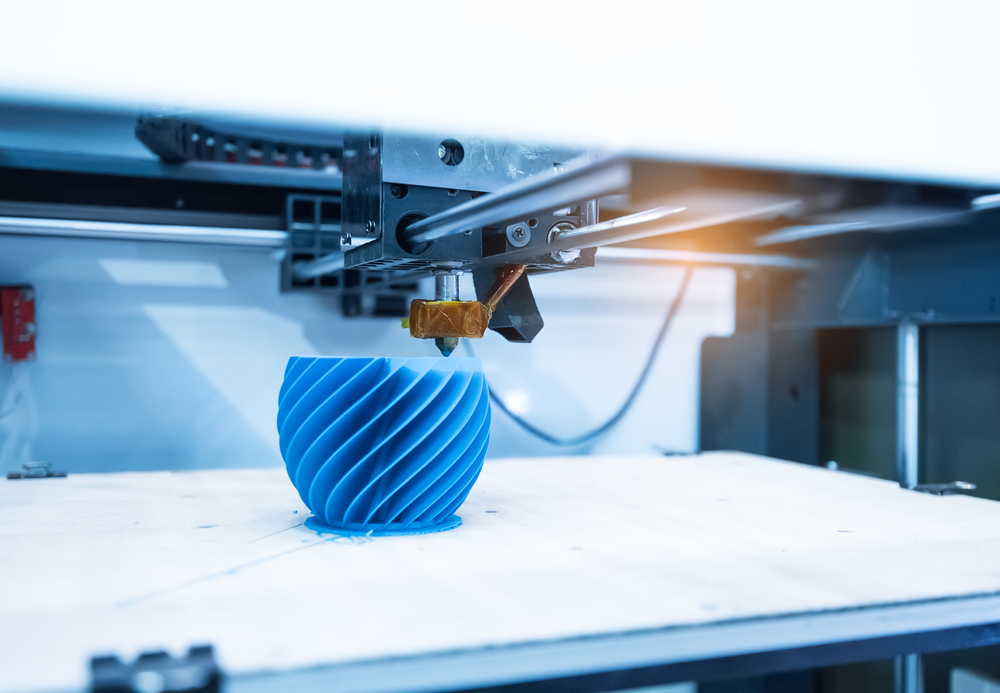
Prototyping: Refining and Testing Your Design
Once you have a general idea, you can move into a more detailed prototyping phase. This stage allows you to test and refine the design before committing to full-scale production. 3D printing offers the flexibility to make minor or significant adjustments without the lead time associated with traditional manufacturing methods.
Steps to Implement:
- Use different materials to simulate the final product’s feel and durability. For example, if you’re designing a wearable, consider materials that mimic the textures of the final product.
- Print functional prototypes to test moving parts, hinges, or assembly components. High-resolution FDM printers like those at Concept 274 can produce accurate details, making it easier to test real-world functionality.
Benefits: This stage helps identify potential design flaws and ensure all parts work together as expected. Rapid prototyping means you can test multiple iterations in days instead of months, saving time and money.
Iterative Testing: Improve Based on Feedback
Feedback is a cornerstone of effective product development. Whether from your team or actual users, feedback allows you to refine your design and make it truly user-centric. 3D printing makes incorporating these insights easy and reprinting an improved version quickly.
Steps to Implement:
- Gather feedback on the prototype’s usability, aesthetics, and functionality. Make a note of any recurring issues or preferences that testers highlight.
- Use 3D printing to update the prototype based on this feedback. Rapid turnarounds mean you can test multiple variations without interrupting the workflow or waiting on outside vendors.
Benefits: With 3D printing, each piece of feedback is a step closer to a market-ready product. The quick turnaround fosters a collaborative, agile environment, encouraging team members to share ideas openly.
Manufacturability Assessment: Ensuring a Smooth Transition to Production
Before committing to large-scale production, evaluating whether your design is manufacturable is essential. This step helps avoid costly design modifications later in the process. 3D printing is a valuable tool for bridging the gap between design and production.
Steps to Implement:
- Print a final prototype that mirrors production-ready specifications. This model allows you to assess manufacturability, assembly, and finishing processes.
- If working with external manufacturers, share the prototype to receive feedback on any adjustments needed for mass production.
Benefits: Using 3D printing as a bridge to production ensures that the final product will be functional and aesthetically pleasing. It also minimizes surprises during the manufacturing phase, reducing delays and additional costs.
Small-Batch Production: Bridging the Gap Between Prototype and Full-Scale Production
Sometimes, producing a limited run before going full-scale is beneficial, especially for startups or companies testing market response. 3D printing is perfect for these low-volume manufacturing needs.
Steps to Implement:
- Produce a small product batch using high-quality, durable 3D printing materials. This step provides a realistic preview of the product’s appearance and performance in the market.
- Distribute the batch to early adopters or beta testers to gauge market interest and gather real-world data on performance.
Benefits: Low-volume production enables you to test the waters without a full commitment. It’s also an opportunity to generate buzz and gather feedback that can inform the final iteration before a full launch.
Post-Launch Iteration: Adapting Quickly to Market Demands
Products may require updates based on customer feedback or emerging trends even after launch. Instead of relying on lengthy retooling processes, 3D printing allows you to iterate and improve post-launch efficiently.
Steps to Implement:
- Use customer feedback to identify any minor tweaks or upgrades.
- Quickly produce updated versions or complementary accessories that meet new demands, such as custom brackets or add-ons.
Benefits: The ability to respond quickly to market demands keeps your product relevant and can differentiate you in competitive markets. For example, wearable tech companies often use this approach to improve fit or functionality based on user feedback.
Conclusion: Realizing the Full Potential of 3D Printing in Product Design
By integrating 3D printing into each stage of the design process, from concept through to post-launch iteration, product designers can save time, reduce costs, and create innovative solutions that resonate with users. At Concept 274, we specialize in guiding product designers through this integration, ensuring that every stage maximizes the potential of 3D printing technology.
Ready to incorporate 3D printing into your design process?
Book a consultation, and let’s bring your ideas to life efficiently, precisely, and quickly.